Automation of Wine Process Filtration
A growing business has many facets to manage, from finances and administration to equipment and personnel. Torresan Estate (TE) in McLaren Vale has grown significantly in recent years, and has had to keep on top of all of these aspects of the business. Nevertheless, strain was beginning to show as core staff had to work longer and longer days to keep up with production. As the business improved and the workday lengthened, the prospect of staff having to spend an additional 2-3 hours in preparation of the bottling line for the following day grew less and less tolerable. Without putting on another full production shift, how then could Torresan Estate improve production efficiency and maintain business and personal sustainability?
The problem
The primary problem for Torresan Estate was one of severe impacts on staff time and the subsequent impact of this on life quality due to the manually operated filtration skids in use. The existing main filtration skid had also reached the limitations of its capacity and, given that the Line 2 filler was also being upgraded, a high flow filtration skid was necessitated. Since no suitable filtration system was available “off the shelf” that was capable of addressing all of the specific requirements of Torresan Estate in terms of design, flexibility, redundancy and remote access, Blue H2O Filtration (BHF) was engaged to design and fabricate a bespoke automated filtration system, with significant and ongoing consultation with Torresan Estate throughout the process to ensure concept integrity.
The requirements for the new BHF Automated Filtration System (AFS) were manifold:
> Automation, encompassing different production filtration modes, cleaning, sanitization, sparging, blow-down and N2 purging of filtration vessels and wine.
> Remote access from multiple devices
> Integrated integrity testing
> Filtration capacity increase, to couple with the upgraded filler for Line 2
> Full integration with both the new filler and existing clean-in-place (CIP) systems.
> Independent white and red filtration lines
> Integral heat exchanger to modify wine temperature to optimize filtration flow to filler (if required)
> A maximum footprint of 1.5 x 5 m, owing to space limitations in the production area. This requirement, along with those aforementioned, made the system design a major exercise in innovation.
Filtration design
First and foremost, the AFS was designed to filter wine at a rate suitable for the new filler. There are three filtration options for any wine according to user selection:
> Coarse stainless mesh (white and red lines)
> Fine particulate polish (red line only)
> Sterile filtration (white and red lines)
All wines being packaged are filtered through at least one of these options, and all wines pass through the mesh filters, which are a final failsafe precaution prior to the filler. The AFS design is duplex, so one white train and one red train. While mesh and polish filtration are relatively simple, sterile filtration is more complex, necessitating 3 filtration stages and 4 filter housings (plus mesh) to retain process efficiency.
The first sterile train housing, the prefiltration stage, utilises a proprietary pleated cartridge filter assembly in an all-polypropylene (PP) filter format with microbial retention that can be repeatedly caustic-regenerated, backflushed and sanitised. This is important, since this filter takes the primary filtration load in the sterile filtration train. Moreover, this multi-cartridge housing is oversized to further improve prefiltration performance efficiency, filter longevity and to maintain a suitable flow rate to the subsequent housings. This approach proved its worth in the first 2 months of operation, with a notable decrease in filter usage. The prefiltration stage is duplexed on both white and red lines, so that if the prefilters block the system can automatically switch itself to the alternate prefilter housing in the train, referred to as duty/standby configuration. In this way production does not stop in the event of a prefilter blockage. Once the system switches to the alternate prefilter housing, the blocked housing automatically goes into a cleaning cycle, and when complete it remains in standby mode ready to serve should another blockage occur.
The second component of the sterile train is a multi-round cartridge housing containing proprietary PES prefilter membranes. The primary purpose of these filters is to provide protection for the sterile membranes in the final housing.
The final housing in the sterile train is also a multi-round cartridge housing containing sterile grade PES final membranes. These are high area dual layer integrity testable membranes and constitute the final barrier to microorganisms prior to the filler. Given the cost of these filters, and more importantly the down-time associated with changing them out/sanitising/integrity testing in the event of a blockage, careful consideration was given to this and preceding filter types. Additionally, since the final membrane and membrane prefilter housings have no redundancy, unlike the PP prefilters, screening of wines to be sterile filtered using wine filterability analysis (see, for example: Bowyer et al, 2012; Bowyer et al, 2013; Bowyer and Edwards, 2014; Bowyer and Edwards, 2018) is of paramount importance to ensuring minimal production downtime and maximum filter life.
System design
The reality of what is required to achieve high level automation of an already complex filtration skid is rather confronting. A bird’s-eye and perspective images of the actual BHF Automated Filtration System are presented in Figure 1 below. The footprint restriction of 1.5 x 5 m required significant design consideration, and a highly condensed system in spatial terms.
(a)
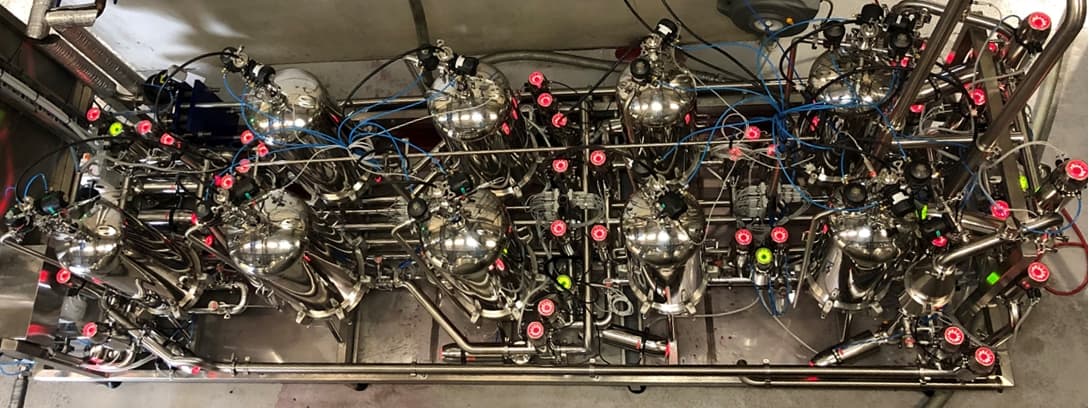
(b)
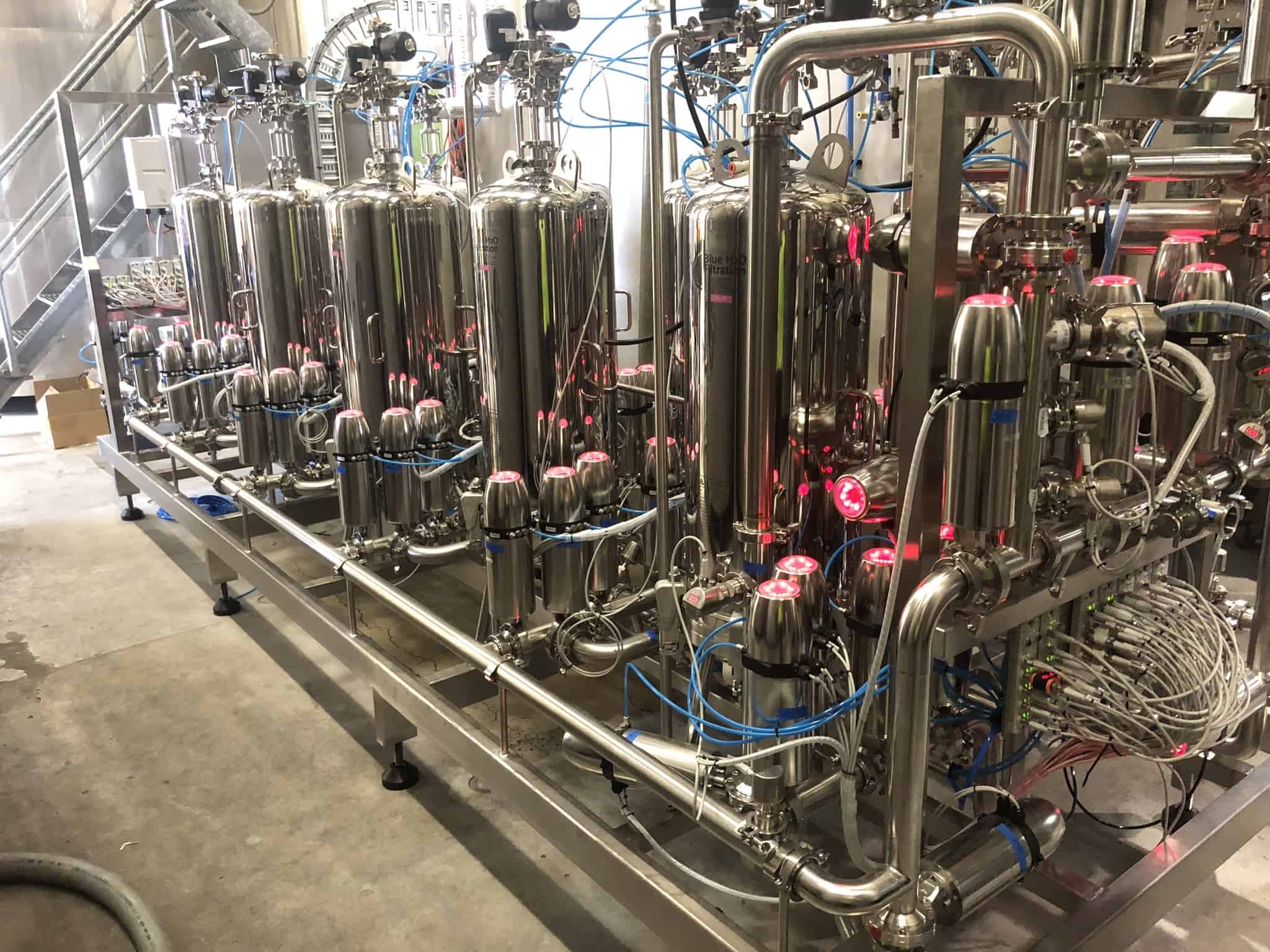
Figure 1. (a) A bird’s eye view of the Line 2 AFS, showing the unit during operation. The wine inlet, control panel cabinet, pump and heat exchanger are at left, and the wine outlet at right. (b) a ground-level view of the AFS.
Immediately obvious are the LED lights throughout the skid, which are compressed air actuated valves controlling the programmed wine flow path. Wine flow is controlled through a combination of the pipework, actuated valves and programmed actuation sequences, governed by BHF’s integrated Programmable Logic Controller (PLC). Red indicates a closed valve and green indicates open valve operation. Filtered compressed air is used to actuate valves, and high purity nitrogen (generated onsite and powered by the site photovoltaic array to minimise environmental impact) is used for the purging of housings to minimise oxygen pickup. Nitrogen is also used to purge wine from housings to the filler at the end of a filtration run, minimising wine losses and oxygen pickup, which is very important to both Torresan Estate and their customers.
System capabilities
COMMUNICATIONS
The filtration system is fitted with a PLC for control, and an Ethernet/IP interface is provided for integration with CIP and filler systems. Heartbeats are provided to prove communications links are healthy (Figure 2). The heartbeat bit is toggled every 10 seconds. In this manner the AFS maintains constant integrated communications with both the existing CIP and filler systems, so that all three systems can function as discrete or fully integrated units. In the event of a system alarm, the PLC displays the alarm on the Human-machine interface (HMI) and can send SMS messages to up to 3 devices. The HMI can be mirrored on a smartphone/tablet/computer at any time.
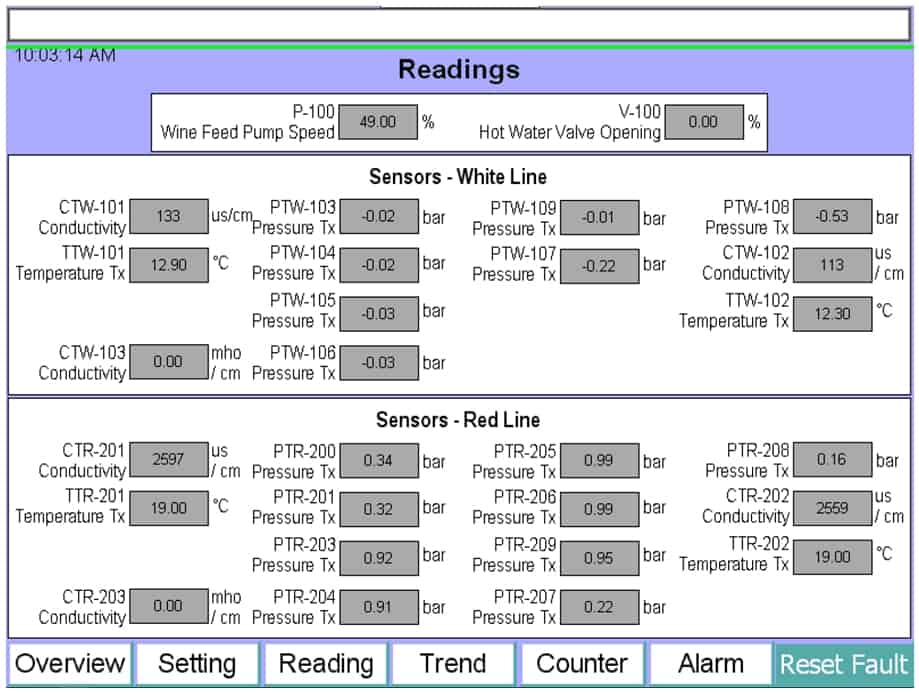
Figure 2. An example of the sensor data parameters logged continuously on the AFS.
CIP SYSTEM AND FILLER INTEGRATION
The CIP HMI, which is remote from the CIP tanks and PLC, can be seen at left in Figure 3. The BHF AFS can be seen in Figure 3 at right, and in between in the background the new filler is visible.
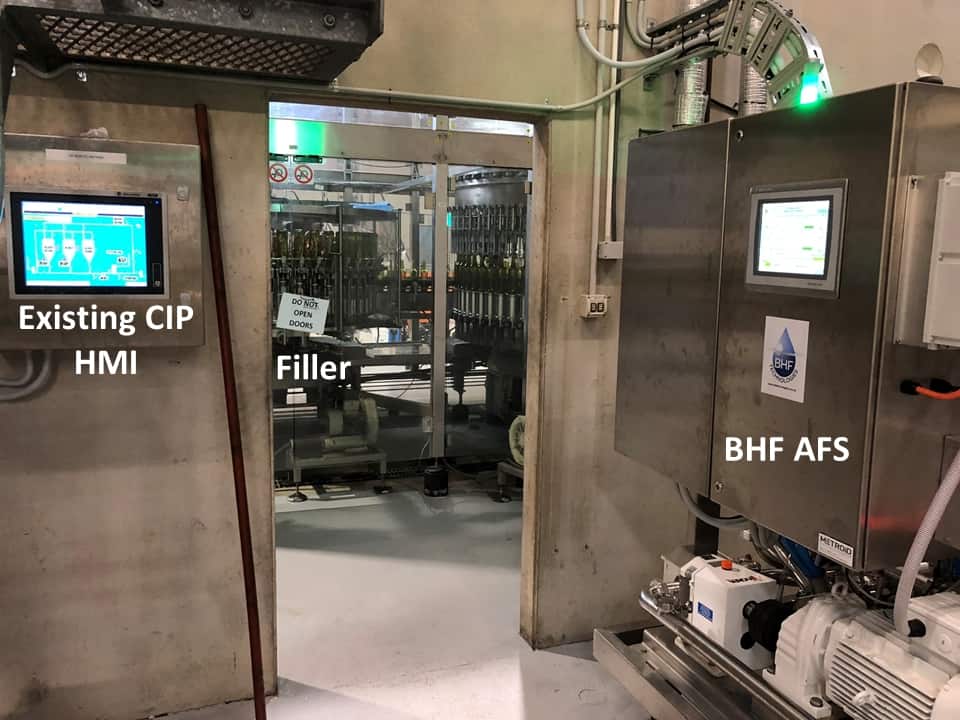
Figure 3. Image showing the positioning of the CIP HMI (left), filler (centre) and AFS (right).
SANITISATION
Since the AFS requires periodic sanitisation to ensure product integrity, detailed and constant parameter logging is required. The AFS logs many sanitisation parameters, including start and finish times, and actual liquid temperatures. The logged data are accessible at any time through the HMI or smartphone mirroring.
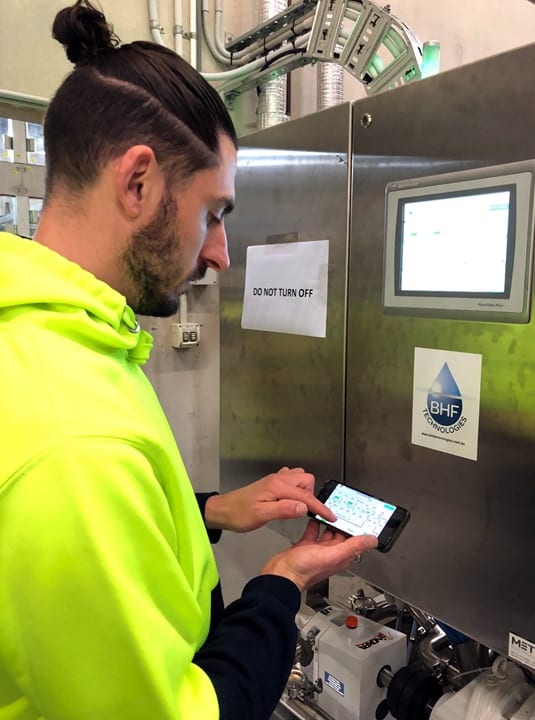
INTERACTIVE PHONE MIRRORING OF THE USER INTERFACE
Since a key deliverable for this project was remote access and the associated liberation of staff time, the AFS was designed to support remote accessibility through smartphone mirroring (Figure 4). All system components that are accessible on the HMI are also accessible via smartphone, tablet or remote computer. This is a critical feature of the AFS, as it allows staff to remotely monitor and command the system without having to be physically present on site.
LIVE MONITORING
At any time the AFS HMI can display all system parameters, accessible by the various system tabs at the lower part of the screen (Figure 5). In this way AFS operation can be monitored at any time either remotely or on site.
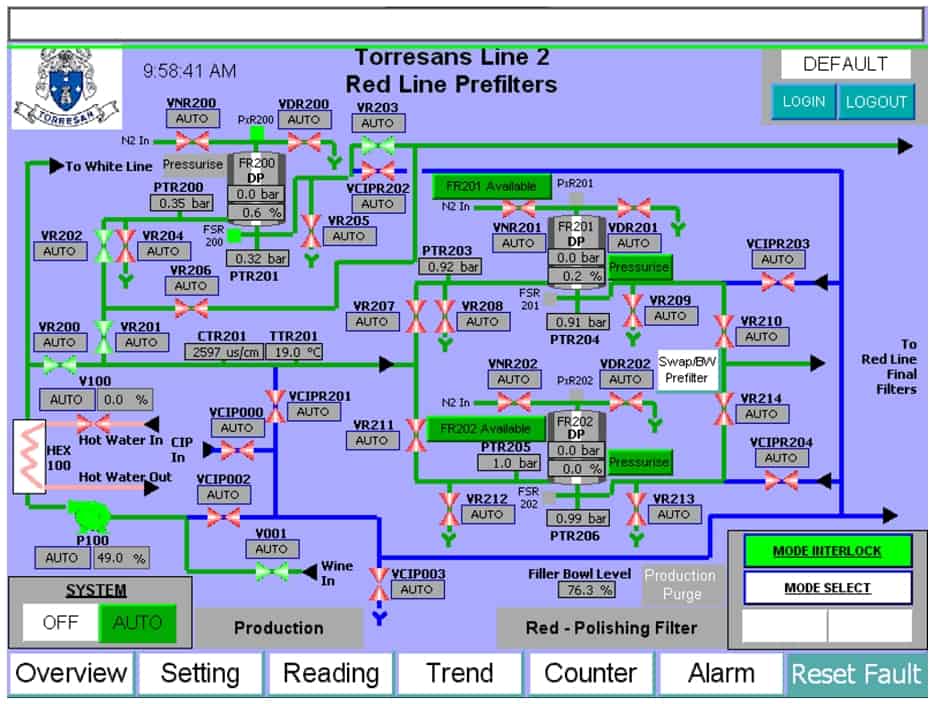
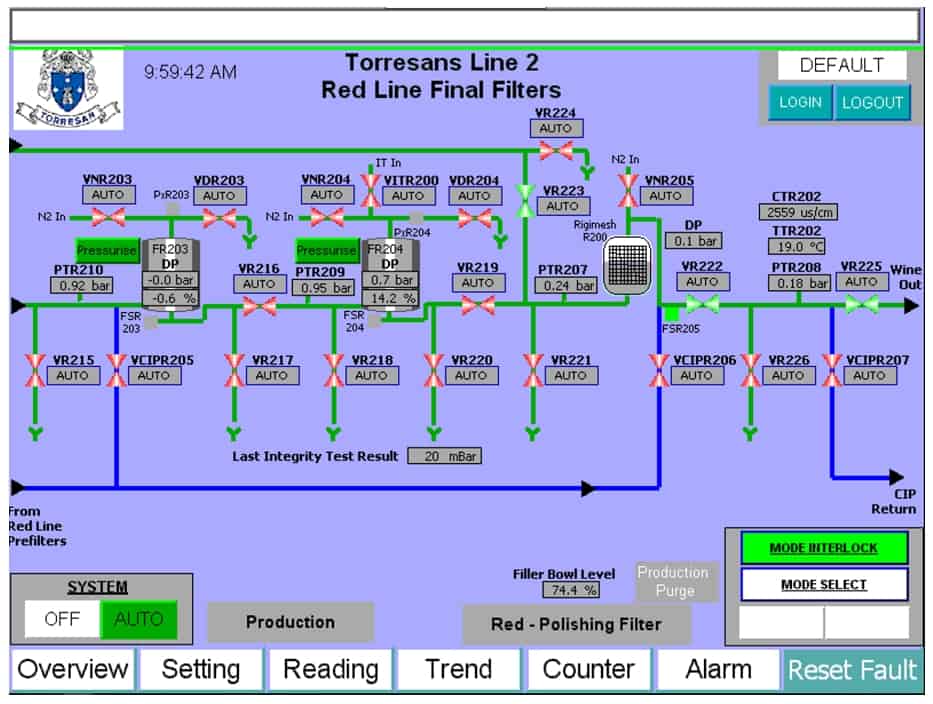
Figure 5. The AFS HMI overview screens. The size and complexity of the system necessitates 2 screenshots to display all system components. (a) Depicts the first part of the system including the prefilters, whilst (b) shows the membrane and mesh housings.
TREND DATA ACCUMULATION
All sensors are logged at 5 second intervals, including pressures, flow rates and temperatures. The data can be exported for use in a spreadsheet. Data can also be viewed in situ via the “Trend” charts on the HMI. An example of trend data display on the HMI is given in Figure 6.
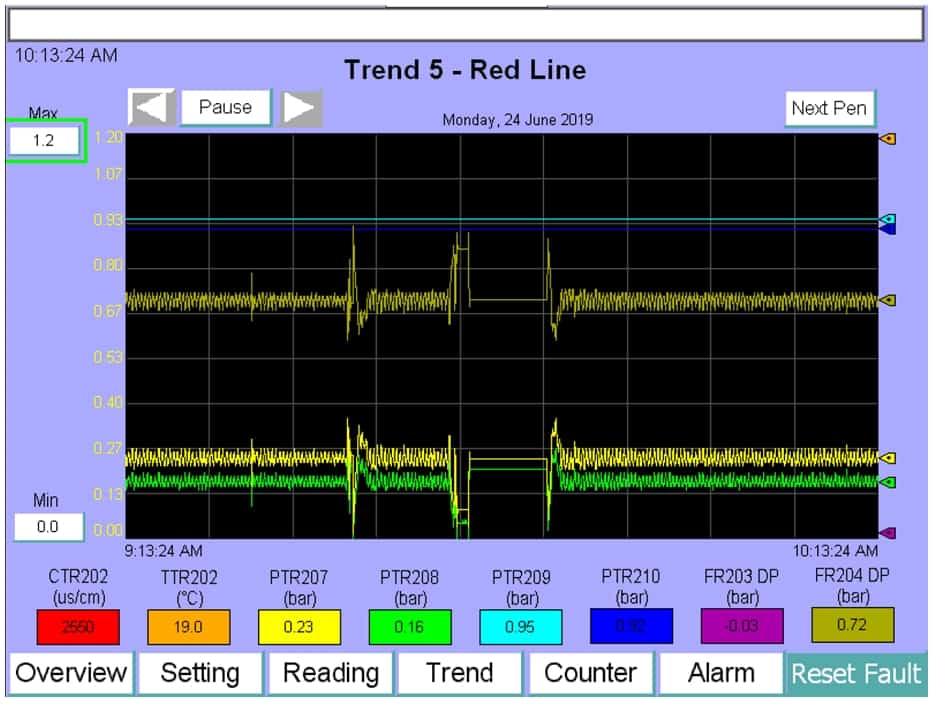
Figure 6. HMI display of trend data on the red line, showing conductivity (CTR), temperature (TTR), pressure (PTR) and differential pressure (DP) data.
So what does it all mean?
Torresan Estate have invested in their efficiency, quality control and sustainability through the BHF Automated Filtration Systems. The ability to fine tune system functionality as required has also provided them with a measure of future-proofing, further enhancing sustainability. As with any complex machine, the AFS must be monitored to ensure system efficiency and proper function, which is made easier through the remote access technology. BHF also maintains a regular site presence to facilitate physical inspections. Lastly, quality control has been improved through the AFS, facilitated by the programmed operation modes, which provide process security.
Wayne Shub, founder and Managing Director of BHF adopted the AFS project with TE under his design and supervision. Wayne and his team are proud of the successful AFS plants at Torresan Estate (and elsewhere) and together shared in the WISA 2019 Packaging Wine Industry Impact Award (Figure 7).
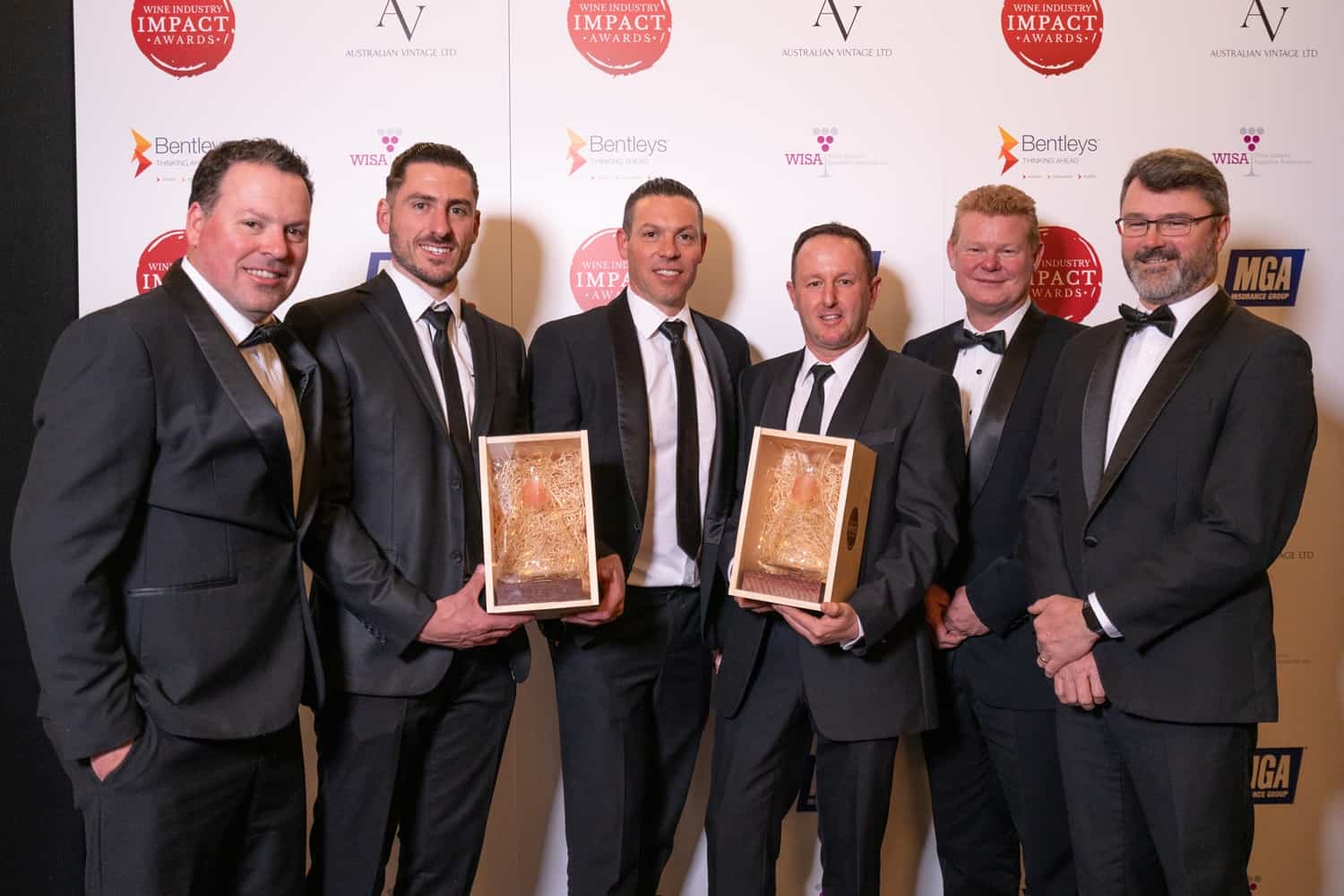
Figure 7. Blue H2O Filtration and Torresan Estate: Winners of the 2019 WISA Wine Industry Impact Award for Packaging for the innovative AFS.
Final words
The three Torresan brothers are pictured in Figure 8 with their new skid. The additional Line 1 AFS has since been installed and is operational. Perhaps it is best for them to have the final words here.

Figure 8. The Torresan brothers from left to right, Julian, Daniel and Damian, in front of the BHF AFS.
Damian Torresan: “We had family members who were spending 16 hours a day at work and this placed significant and unwelcome demands on personal time. By the time the line had finished its work for the day it would then be a 2-3 hour operation flushing filters and sterilizing, plus another 1-2 hours if we had to decolorize from red to white. In trying to quantify time savings to gauge improved capability and competitiveness, we would estimate around 24 operational hours saved each week through the new AFS. Without the new AFS, and if we eliminated family members working overtime for hours each day, we would need to hire an extra 2 – 3 people to be here on an afternoon shift to cover the work. To evaluate the AFS in this way is to miss the point, however. For us, payback was immediate, as we have got our lives back, and that was worth our investment in this process with BHF. The monetary payback pales into insignificance when we evaluate quality of life gains.
“We are fortunate that we have a collaborative partner in BHF. I want to thank Wayne and his team for listening to us and understanding our needs and vision, for making this happen and bringing this to such elegant and functional fruition.”
Daniel Torresan: “In addition to Damian’s comments, another aspect is that we can’t run this operation personally forever, and we need to be able to hand over at some stage to other staff. If process problems were to arise this would seriously compromise Torresan Estate business security and sustainability. This has been overcome to a large extent by the autonomy provided by the BHF AFS. Our old system had manual valve operation and no programming, and so the process risk was high. The BHF system has eliminated this risk through programmed sequencing, and we are much more comfortable in training others knowing that this level of security is in place. It is almost childproof, which is perfect for retaining process confidence.”
Julian Torresan: “In addition to the comments made by Damian and Daniel, which I echo, I would add another angle. On the old filtration system, in any given operational period we would have observed filter degradation and blockage, which would have resulted in significant downtime, filter costs and efficiency loss. With the new system in place, filter life has improved significantly, and that was obvious within the first two months, which is a big gain for us. This basically comes down to superior system design and functionality, and is a benefit beyond the gains that the system automation provides. We have also observed less wine loss than previously, which is important to us and our customers.
“The time savings permitted by the remote access and control features of the BHF Filtration System have produced a strong efficiency gain for the business, giving us more flexibility and the ability to correct any issues even if we are not on site. We can monitor system functionality online anytime, anywhere. The sanitisation process is now just a matter of selecting a programme. The system will perform the sanitisation and finish automatically, ready for operation the next day, so we can now make full use of our personal time. BHF also have the capability to make system adjustments remotely, and we have already made use of this in fine-tuning the system parameters to our requirements. This is a great advantage to the sustainability of the business.”
By Paul Bowyer, Wayne Shub, & Steve Brunato
References
Bowyer, P. K., Edwards, G. and Eyre, A. (2012) The Australian and New Zealand Grapegrower and Winemaker, NTU vs. wine filterability index – what does it mean for you? Issue 585, 76-80.
Bowyer, P. K., Edwards, G. and Eyre, A. (2013) The Australian and New Zealand Grapegrower and Winemaker, Wine filtration and filterability – a review and what’s new, Issue 599, 74-79.
Bowyer, P. K. and Edwards, G. (2014) The Australian and New Zealand Grapegrower and Winemaker, Understanding filterability index: an overview and some new insights, Issue 610, 80-85.
Bowyer, P. K., Edwards, G. and Eyre, A. (2018) The Australian and New Zealand Grapegrower and Winemaker, Filtration tips: an in-depth discussion, Issue 658, 48-56.
BHF wishes to thank The Australian and New Zealand Grapegrower and Winemaker for permission to reproduce this article. Subscription information can be found here.